
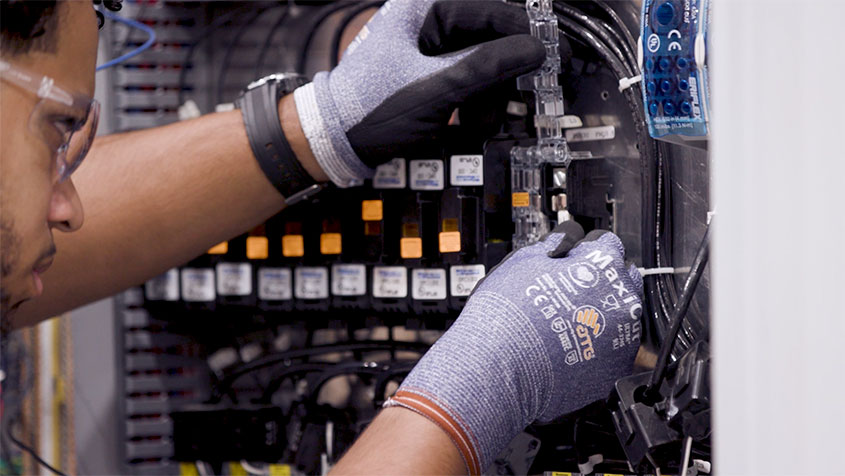
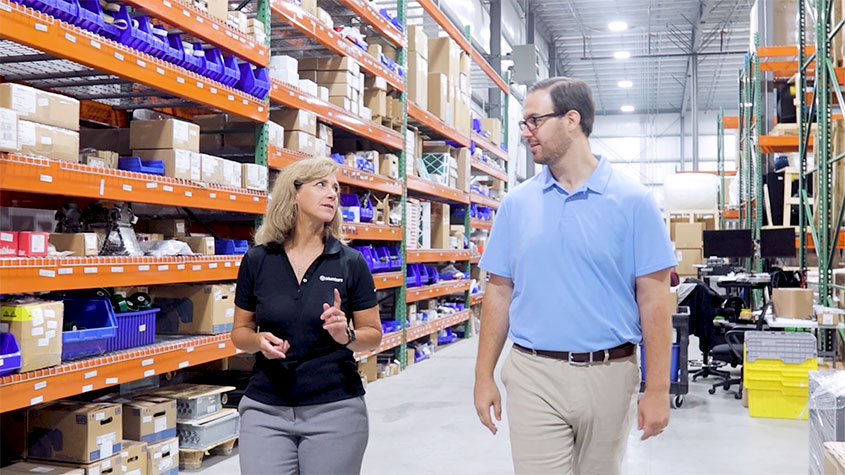


Sponsored by Munters.
As the electric vehicle (EV) market continues to grow gigafactories are multiplying across the globe. These enormous production facilities, tasked with producing the batteries that power EVs, represent a crucial hub of innovation. However, beyond the scorching summer temperatures that dominate headlines, gigafactories face a hidden enemy: rising humidity.
The hidden challenges of summer for gigafactories
While sunshine and warmth may characterize the season for many, these large-scale facilities dedicated to lithium-ion battery production for electric vehicles require stringent environmental controls, particularly regarding moisture levels. Lithium-ion batteries are highly sensitive to even minor fluctuations in dew point. Uncontrolled humidity during the summer months can have a significant impact on gigafactory operations.
A domino effect of excessive moisture
Increased moisture load strains dehumidification systems and their make-up air handlers. If these systems haven’t received the necessary proactive maintenance, they may struggle to maintain the ultra-low dew point requirements crucial for optimal battery production. This can lead to dry rooms falling short of their specified conditions, potentially resulting in product quality issues or unplanned downtime.
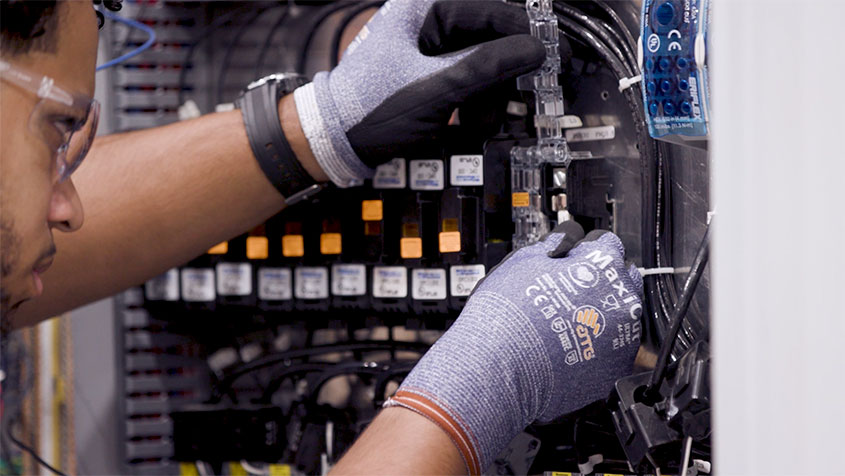
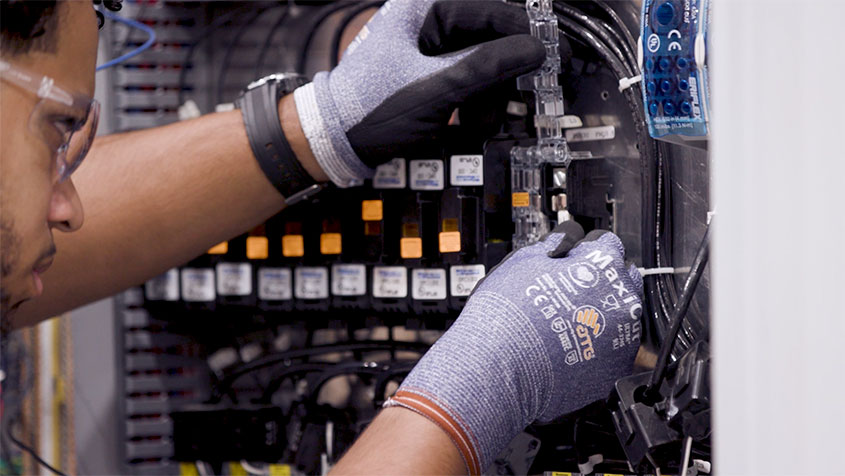
Optimizing uptime and efficiency with spare parts
While proactive maintenance is paramount for dehumidification systems, Tim Lawler, Service Product Manager for Munters Americas, emphasizes the importance of a strategic approach to spare parts: “Maintaining a spare parts inventory is crucial year-round. However, during the summer months, the equipment operates closer to its maximum capacity to meet the ultra-low dew point requirements of Battery dry rooms. There is considerably less margin for performance issues; what might seem like a minor performance degradation in the winter could become a significant problem on an extremely humid day in summer. While on-site spare parts inventory cannot substitute for proactive maintenance, it can reduce downtime by having the necessary parts readily available if an issue was to arise.”
A collaborative approach to spare parts management
A key aspect of Munters’ approach to spare parts is collaboration. A dedicated back-office service team works closely with gigafactories throughout the equipment lifecycle. This dedicated team of experts ensures gigafactories have the necessary on-site inventory to maximize uptime and meet routine maintenance needs. With readily available spare parts, issues can be addressed promptly, minimizing downtime and production delays.
Shared parts, reduced burden
Understanding the complexities of managing vast inventories in gigafactories, Munters has designed its LDP and ICA dehumidifiers with common parts. This intentional design minimizes the need for extensive customer inventory and simplifies equipment serviceability. In gigafactories housing upwards of fifty dehumidification units and tens of thousands of additional pieces of equipment, this shared parts approach significantly reduces operational burdens for lithium-ion battery production facility managers.
Learn more about taking the guesswork out of spare parts replacement.
Optimizing performance year-round with proactive service
While spare parts are crucial, Munters prioritizes a proactive service approach that extends beyond mere component replacements. Tim Lawler emphasizes: Munters’ objective is to reduce the necessity of using this spare inventory through the implementation of a proactive service strategy. While spare parts are crucial for maintaining dehumidification equipment, they are only one aspect to consider. Munters Service Agreements allow us to provide proactive recommendations to maximize uptime, maintain performance, and optimize efficiency.
Comprehensive on-site service: Gaining actionable insights
Munters’ service agreements provide gigafactories with a comprehensive on-site service experience. Highly trained Munters technicians utilize state-of-the-art, calibrated instruments, gauges, tools, and proprietary software to perform a thorough analysis of your dehumidification system’s performance. This analysis goes beyond simply verifying operation. Technicians meticulously inspect all components, including the Munters-produced desiccant wheel, to ensure optimal functionality.
Empowering decisions with detailed reports
Following the comprehensive on-site inspection, Munters delivers a detailed service report packed with actionable insights and recommendations. It highlights specific system components that require ongoing monitoring to ensure smooth operation.
Based on their analysis, Munters service technicians may recommend modifications, repairs, or replacement parts to address any potential issues before they escalate into bigger problems. Additionally, the report provides a customized routine maintenance schedule tailored to each system’s specific needs.
Munters may suggest adjustments to service parameters or operating settings to optimize dehumidification system performance and efficiency. This comprehensive report enables gigafactory managers to proactively address potential issues and ensure your system operates at peak efficiency.
Benefits of pre-summer proactive service
Securing a Munters Service Agreement as we approach summer offers significant advantages. Their proactive service approach allows Munters to identify and address potential issues in your dehumidification system before the increased humidity of summer arrives. With a Munters Service Agreement in hand you can minimize the risk of performance issues or unplanned downtime.
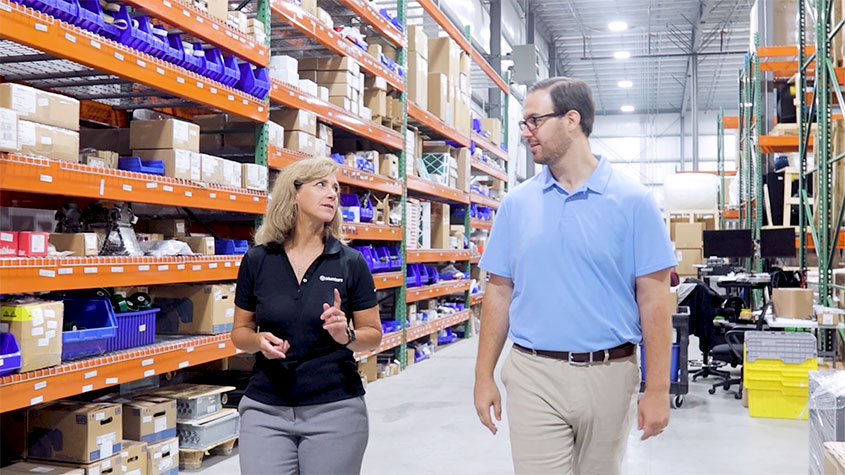
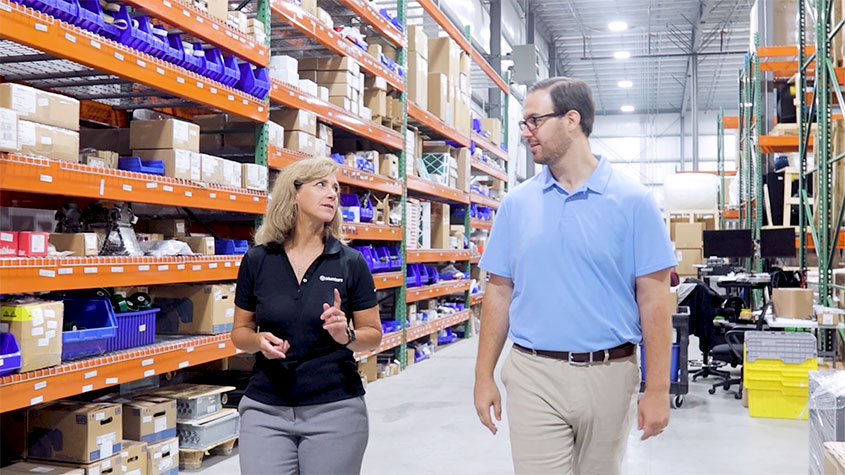
Year-round support
Munters Service Agreements provide ongoing support throughout the year. This comprehensive approach can give gigafactories peace of mind, knowing they are prepared for the unique operational challenges of each season, allowing them to focus on what matters most: seamless lithium-ion battery production. By combining a proactive service strategy with readily available spare parts, Munters empowers gigafactories to operate at peak efficiency while minimizing downtime.
Summer service tips from Munters Service Project Manager Tim Lawler
As summer approaches, maximizing the efficiency of your dehumidification system becomes paramount. Here are key actions I want to recommend that will ensure optimal performance throughout this hot and humid season:
- Prioritize preventive maintenance
Don’t wait for summer to discover maintenance needs. Schedule regular maintenance tasks according to the manufacturer’s recommendations to guarantee your dehumidification system operates at peak capacity before the increased workload hits. Preventive maintenance can help identify and address minor issues before they snowball into larger problems during peak summer demand. - Verify and test redundant units
Gigafactories often rely on redundant dehumidification units as a safeguard against unexpected downtime. Conduct periodic test runs of these backup units to verify their functionality. This ensures a smooth transition if a primary unit experiences an issue during peak summer demand. Testing also helps identify any potential problems with the redundant units themselves, allowing for timely repairs or replacements. - Maintain a critical spare parts inventory
Operational disruptions due to failed or worn components can be costly. Therefore, it is crucial for a gigafactory’s storeroom to be equipped with essential spare parts to mitigate the risk of unit shutdowns or performance degradation.Munters can help identify critical spare parts and consumables required for routine maintenance, aligning with the specific equipment and operational requirements of each facility. By proactively managing inventory, customers can ensure operational readiness not only for the summer season but for continuous efficiency throughout the year.
- Partner with a dehumidification expert
By following these simple steps and partnering with a dehumidification expert like Munters, gigafactories can face any season with confidence, knowing their dehumidification system is prepared to deliver optimal performance and contribute to the seamless production of high-quality lithium-ion batteries.
Meet Tim Lawler
Tim Lawler is a Service Product Manager for Munters with eight years of experience in the industry. Tim develops services tailored to our customers’ needs that help battery factories of all sizes achieve their goals. Tim is passionate about ensuring gigafactories have the resources and support they need to operate efficiently and contribute to a sustainable future.
About Munters
Munters has been servicing battery manufacturers, while working with contractors, and A&E firms for over 40 years. They specialize in dry room manufacturing space climate control with proven desiccant dehumidifier technology, to maintain consistent, accurate dew point levels in production facilities of all sizes. With a global network of experienced professionals and strategically located warehouses, Munters offers unparalleled support to gigafactories around the world. Contact Munters today to learn more about how they can help your gigafactory gear up for summer and achieve optimal battery production efficiency.

Source link
#gigafactory #ready #summer