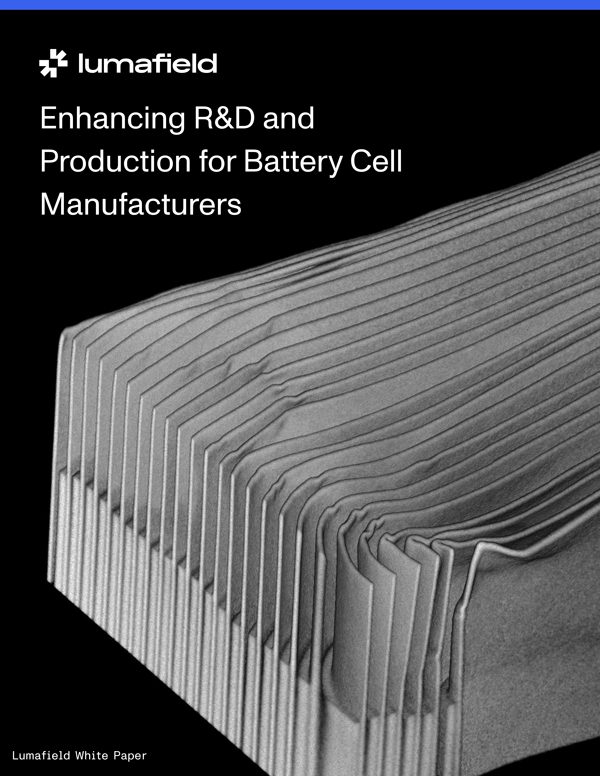
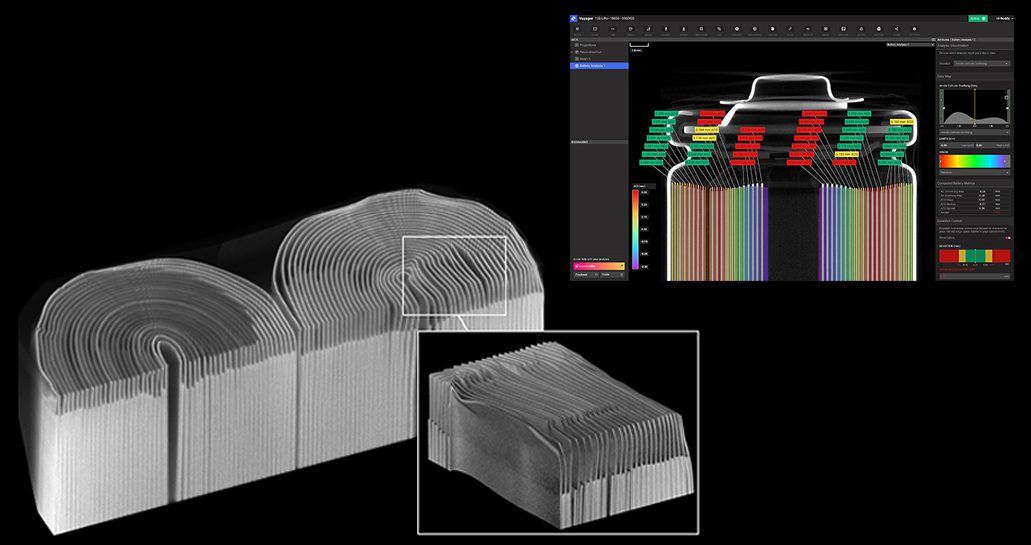
As the battery industry is projected to surpass $300 billion by 2030, driven by the rise of electric vehicles and renewable energy storage, manufacturers face the dual challenge of rapid innovation and stringent quality requirements. Traditional testing methods often fall short in detecting internal defects or optimizing complex designs. CT scanning addresses these challenges by providing non-destructive, detailed internal visualizations of battery cells, enabling engineers to find misalignments, folds, tears, and other internal defects without disassembling the cell. This capability accelerates development, enhances reliability, and supports faster innovation cycles.
In research and development, CT scanning is invaluable for accelerating material development by visualizing the distribution of materials within a battery cell, allowing for the early detection of flaws like internal cracking or voids. It also aids in identifying defects in new chemistries and form factors, such as delamination in solid-state batteries or dendrite formation in lithium-metal systems, which are critical for ensuring performance and safety before large-scale production. By integrating CT scanning into both R&D and production processes, battery manufacturers can enhance quality control, reduce waste, and bring innovative products to market more efficiently. Download this whitepaper to learn more.
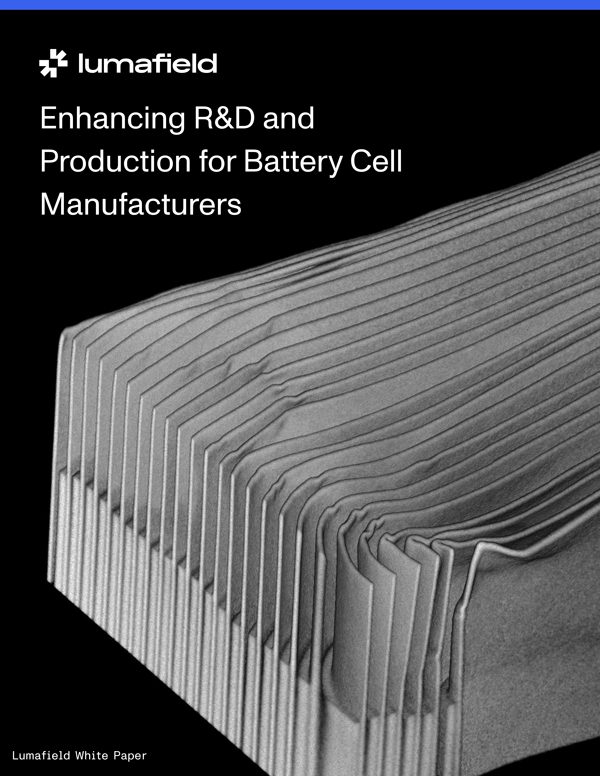
Source link by Charged EVs
Author Charged EVs
#optimize #battery #development #production #technology